Digital Transformation
Digital transformation is the integration of digital technology into all aspects of a business, fundamentally changing how organizations operate and deliver value to customers. It involves leveraging cutting-edge technologies like artificial intelligence (AI), the Internet of Things (IoT), cloud computing, and big data analytics to streamline processes, improve efficiency, and enhance customer experiences.
The Importance of Digital Transformation:
As the world becomes increasingly digital, businesses must adapt to stay competitive. Digital transformation is not just about adopting new technology; it's about reshaping business models, enhancing customer engagement, and ensuring agility in an ever-evolving market landscape.
Key Benefits:
- Enhanced Customer Experience: Personalization, seamless interactions, and real-time responses.
- Operational Efficiency: Automating repetitive tasks and optimizing workflows.
- Data-Driven Decision Making: Leveraging analytics for actionable insights.
- Innovation & Growth: Enabling new business models and revenue streams.
- Increased Agility: Faster adaptation to market changes and disruptions.
What is OEE (Overall Equipment Effectiveness)?
OEE (Overall Equipment Effectiveness) is a key performance metric used in manufacturing to measure the efficiency and productivity of equipment. It provides insights into how well a machine or production line is utilized compared to its full potential.
OEE Formula:
OEE= Availability × Performance × Quality OEE = Availability \times Performance \times Quality OEE = Availability × Performance × Quality
Where:
- Availability = (Operating Time / Planned Production Time)
- Performance = (Actual Production Rate / Ideal Production Rate)
- Quality = (Good Units Produced / Total Units Produced)
Understanding OEE Metrics:
- 100% OEE means perfect production: no downtime, maximum speed, and zero defects.
- 85% OEE is considered world-class in manufacturing.
- 60%-70% OEE is common for many industries, indicating room for improvement.
- Below 50% OEE suggests inefficiencies that need urgent attention.
Components of OEE
1. Availability
- Measures downtime losses due to machine breakdowns, setup, and changeovers.
- Higher availability means minimal stoppages and improved uptime.
2. Performance
- Evaluates if equipment is running at optimal speed.
- Performance losses occur due to slow cycle times, minor stoppages, or reduced efficiency.
3. Quality
- Determines how many defect-free products are produced.
- Quality losses result from defects, rework, or production rejects.
What is Overall Effective Efficiency?
Overall Effective Efficiency (OEEf) is an advanced version of OEE that considers additional factors such as labor efficiency, process optimization, and overall system performance beyond just equipment effectiveness.
OEE vs. Overall Effective Efficiency
Metric | OEE (Overall Equipment Effectiveness) | Overall Effective Efficiency |
---|---|---|
Focus | Machine or equipment effectiveness | Holistic efficiency including workforce and process |
Factors | Availability, Performance, Quality | Includes labor, energy, and production systems |
Application | Manufacturing and industrial machinery | Lean manufacturing, business processes, and service sectors |
How to Improve OEE & Efficiency
- Reduce Unplanned Downtime: Implement predictive maintenance to minimize unexpected failures.
- Optimize Production Speed: Ensure machines operate at peak efficiency with minimal slowdowns.
- Enhance Quality Control: Use AI, automation, and better materials to reduce defects.
- Workforce Training: Equip employees with skills to handle machines efficiently.
- Data-Driven Decision Making: Leverage IoT, analytics, and real-time monitoring for continuous improvements.
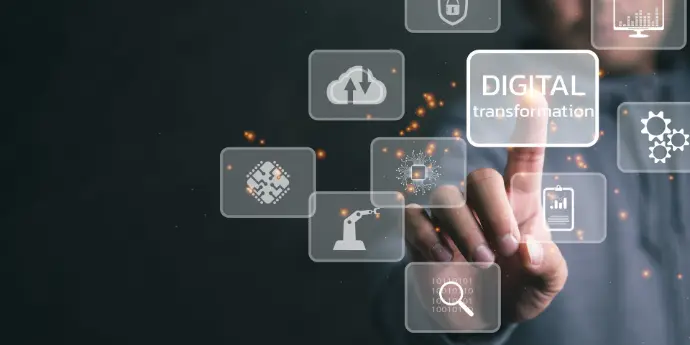
Manufacturing Execution System
A Manufacturing Execution System (MES) is a software solution designed to monitor, control, and optimize manufacturing operations in real time. It bridges the gap between enterprise resource planning (ERP) and the shop floor, ensuring efficient production processes, data accuracy, and operational visibility.
Why is MES Important?
In today’s competitive manufacturing landscape, MES plays a crucial role in driving digital transformation by:
- Enhancing productivity and efficiency.
- Providing real-time data for informed decision-making.
- Ensuring quality control and compliance with industry standards.
- Reducing waste and operational costs.
Key Features of MES
1. Real-Time Production Monitoring
- Tracks machine and labor performance.
- Provides live updates on production status.
2. Work Order & Scheduling Management
- Automates job scheduling for optimal resource utilization.
- Reduces downtime and improves workflow efficiency.
3. Quality Management
- Monitors product quality through inspections and compliance tracking.
- Reduces defects and rework by integrating with quality control systems.
4. Inventory & Material Tracking
- Ensures accurate material usage with real-time tracking.
- Prevents shortages and overstocking with automated inventory control.
5. Data Collection & Reporting
- Provides actionable insights through customizable dashboards and reports.
- Improves transparency in operations by recording key performance metrics.
6. Integration with ERP & IoT
- Seamlessly connects with ERP systems for streamlined operations.
- Utilizes IoT for smart data acquisition and predictive maintenance.
This are the modules we used for MES:
- CRM (Customer Relationship Management)
Odoo CRM empowers businesses with seamless lead tracking, automated follow-ups, and in-depth analytics. It helps manage customer interactions, track sales pipelines, and enhance customer engagement, ensuring a streamlined sales process and improved conversion rates.
- Inventory Management
Odoo Inventory offers real-time stock tracking, warehouse automation, and smart replenishment features. With barcode scanning, batch tracking, and multi-location support, businesses can optimize their inventory operations, reduce waste, and enhance order fulfillment.
- Purchase Management
Odoo Purchase Management simplifies procurement with automated purchase orders, vendor management, and price comparisons. It ensures cost-effective purchasing, enhances supplier relationships, and integrates seamlessly with inventory and accounting for end-to-end supply chain visibility.
- Invoice Management
Odoo Invoice automates invoicing, payment tracking, and financial reporting. With seamless integration with sales and accounting modules, businesses can generate professional invoices, manage payments efficiently, and ensure compliance with financial regulations.
- Sales Management
Odoo Sales provides an intuitive interface for managing quotations, contracts, and sales orders. Businesses can track the entire sales cycle, leverage AI-driven insights, and automate workflows to improve efficiency and drive revenue growth.
- Shop Floor Management
Odoo Shop Floor Management enhances manufacturing operations with real-time production tracking, work order management, and machine performance monitoring. It ensures smooth workflow execution, reduces downtime, and increases operational efficiency.
- Manufacturing Management
Odoo Manufacturing offers complete production planning, BOM (Bill of Materials) management, and work center scheduling. It supports lean manufacturing practices, integrates with inventory and quality control, and enhances productivity with automation and real-time analytics.
Why Choose Odoo for Business Management?
Odoo provides a fully integrated, user-friendly platform that connects all business functions, ensuring streamlined processes, improved efficiency, and scalable growth. From CRM and sales to inventory and manufacturing, Odoo offers a complete solution to optimize operations and enhance profitability.
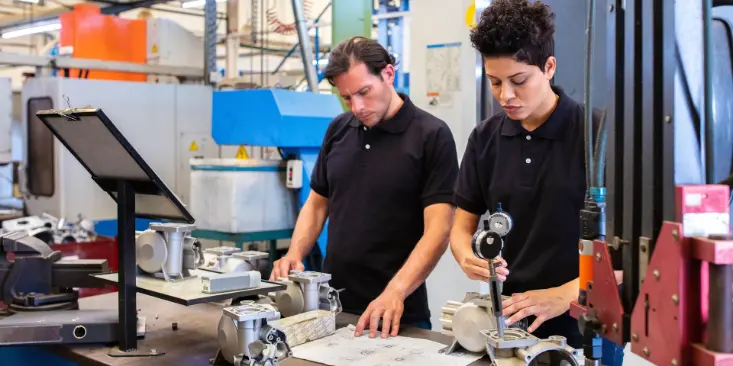
Smart Inventory Management
Smart Inventory Management in Odoo 17 is a powerful, automated solution designed to optimize stock control, streamline operations, and improve supply chain efficiency. With advanced features like real-time tracking, AI-driven demand forecasting, and seamless integration with other Odoo modules, businesses can reduce waste, prevent stock shortages, and enhance productivity.
Key Features of Smart Inventory Management in Odoo 17
1. Real-Time Inventory Tracking
- Utilize barcode scanning, RFID, and IoT sensors for accurate stock levels.
- Instantly update inventory across multiple locations and warehouses.
2. Automated Stock Replenishment
- Set up minimum and maximum stock levels for auto-replenishment.
- Use AI-driven demand forecasting to predict future stock needs.
3. Multi-Warehouse Management
- Manage multiple warehouses from a single platform.
- Optimize stock transfers and warehouse space utilization.
4. Seamless Integration with Odoo Apps
- Connect with Sales, Purchase, Manufacturing, and Accounting modules.
- Ensure accurate stock updates and streamline order processing.
5. Batch & Serial Number Tracking
- Track product batches and serial numbers for quality control.
- Ensure compliance with regulatory standards and traceability requirements.
6. Advanced Reporting & Analytics
- Generate real-time inventory reports with detailed insights.
- Use AI-driven analytics to make data-informed decisions.
Benefits of Using Smart Inventory Management in Odoo 17
- Improved Accuracy & Efficiency: Reduces human errors and manual data entry.
- Faster Order Fulfillment: Enhances customer satisfaction with accurate stock availability.
- Cost Savings: Minimizes holding costs and prevents overstocking.
- Enhanced Decision-Making: Leverages predictive analytics for better inventory planning.
- Scalability: Easily adapts to business growth with modular integrations.
Why Choose Odoo 17 for Smart Inventory Management?
Odoo 17 provides an intuitive, user-friendly interface with robust automation tools that cater to businesses of all sizes. Whether managing a small retail store or a large supply chain, Odoo 17 offers flexibility, real-time data insights, and seamless operations for end-to-end inventory management.
Get Started with Smart Inventory Management in Odoo 17
Upgrade your inventory management with Odoo 17 today. Contact us to learn more about implementation, customization, and how Odoo can revolutionize your business operations.
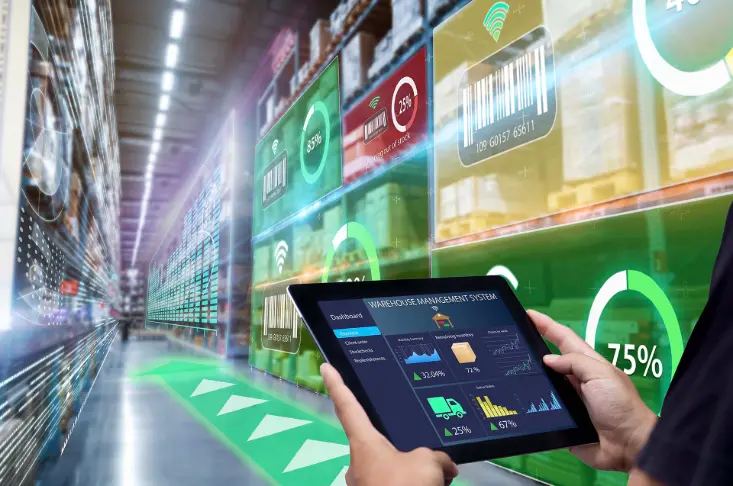
Fleet Management
Optimize Your Fleet Operations with Cutting-Edge Technology
Managing a fleet requires precision, efficiency, and real-time data to ensure smooth operations. Our fleet management solutions provide you with the tools to monitor, analyze, and optimize your fleet performance, reducing costs and improving productivity.
Our Key Features
1. Real-Time Vehicle Tracking
- Stay connected with your fleet through GPS-based tracking. Monitor vehicle locations, routes, and driver activities to enhance security and efficiency.
2. Fuel & Maintenance Management
- Reduce operational costs by keeping track of fuel consumption and scheduling preventive maintenance.
- Get automated alerts for servicing and repairs to prevent breakdowns and downtime.
3. Driver Performance Monitoring
- Improve road safety with detailed driver behavior analytics, including speed tracking, harsh braking, and idle time.
- Encourage responsible driving habits and minimize risks.
4. Compliance & Safety Management
- Ensure adherence to industry regulations with automated compliance tracking.
- Maintain vehicle inspections, licensing, and driver certification records in one place.
Why Choose Our Fleet Management System?
- Cost-Effective – Reduce fuel wastage and maintenance expenses.
- User-Friendly Interface – Easy-to-use dashboard for complete fleet control.
- Scalable Solutions – Perfect for businesses of all sizes, from small fleets to large enterprises.
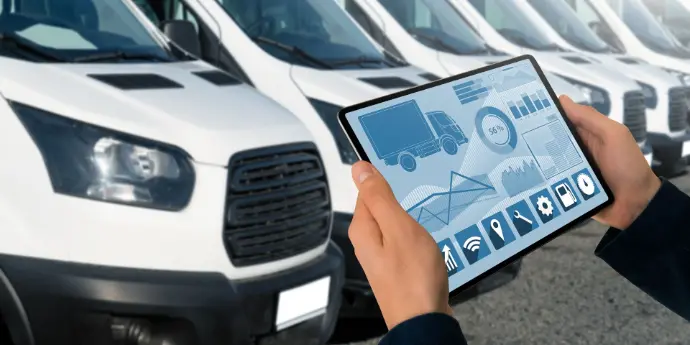